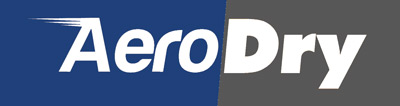
Hoods
Design
Specific designs for different applications in order to meet the project requirements and based on the combustible available at mill site
The yankee hood can be designed to work with gas, steam or thermal oil operation
With a reinforced frame the hood provides high dimensional stability maintaining its geometry in operation during its whole life cycle
Benefits
Production Increase
Quality improvement
Leakage proof ducts sealing
Designed to allow large thermal expansions without hood frame distortions and keeping drying efficiency
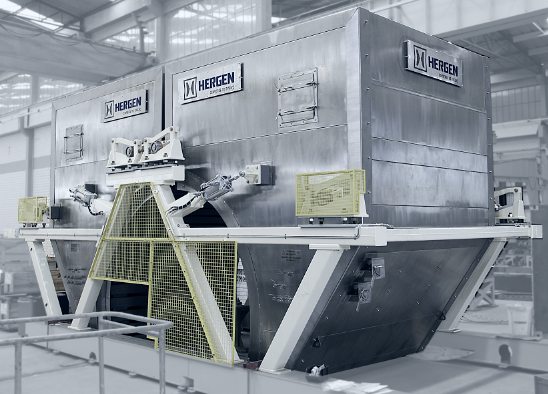
Hoods Line
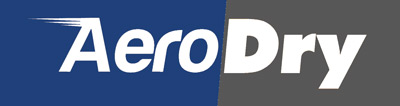
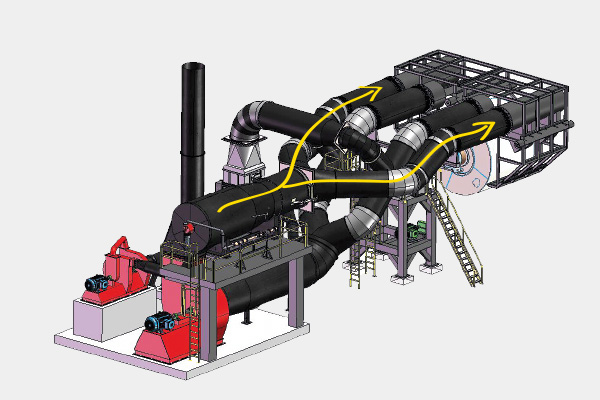
Monosystem gas fired hood

Monosystem
One single hot air line distributed to both hood sides (wet and dry)
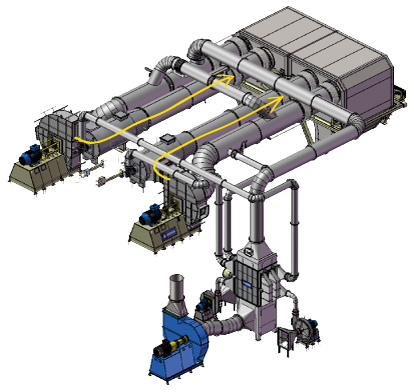
Duosystem gas fired hood

Duosystem
Two independent hot air lines, one for each hood sector allowing an independent temperature control for the dry and wet ends.
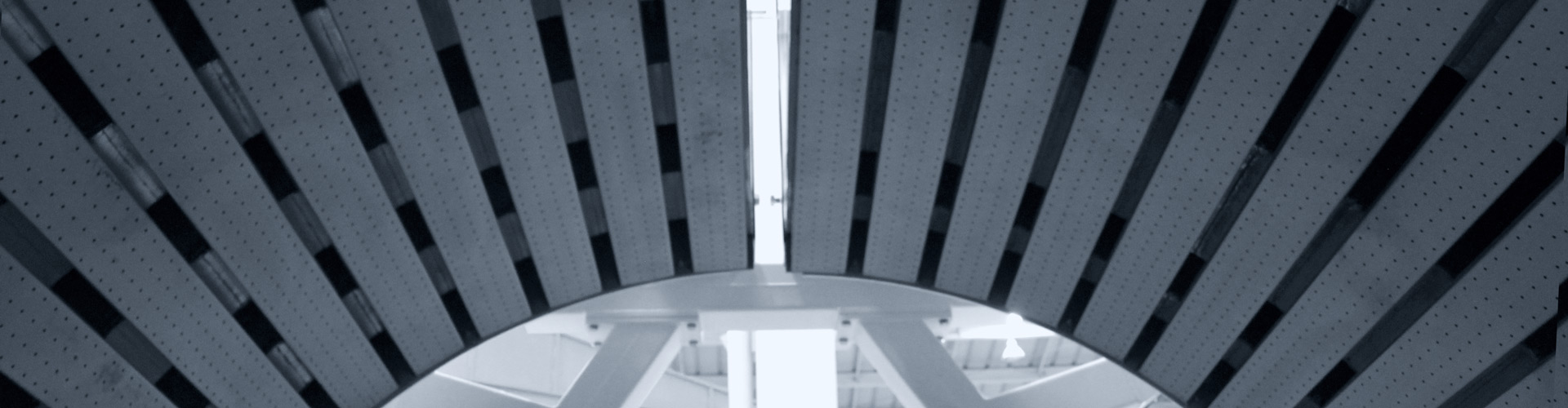